plc编程要会很多种软件吗
Title: Understanding the Maximum Capacity of PLC Programming
In industrial automation, Programmable Logic Controllers (PLCs) play a pivotal role in controlling machinery and processes. PLC programming capacity refers to the maximum amount of logic, instructions, and data that a PLC can handle. Several factors influence the maximum capacity of PLC programming. Let's delve into these factors and understand how to optimize PLC programming efficiently.
1. Memory Capacity:
The memory capacity of a PLC is a primary determinant of its programming limit. PLCs have different memory types, including:
Program Memory:
This memory stores the PLC program, consisting of ladder logic, function blocks, or structured text. The size of program memory varies among PLC models and affects the maximum program size.
Data Memory:
Data memory holds variables, timers, counters, and other data used by the PLC program. The amount of data memory available determines the number of variables and data structures that can be used in the program.To maximize PLC programming, choose a PLC model with sufficient memory capacity for your application. Regularly optimize your code to minimize memory usage, such as reusing variables and optimizing data structures.
2. Instruction Set:
Different PLCs offer varying instruction sets, including basic logic, math, comparison, and communication instructions. The complexity and variety of instructions impact the size of the program. Utilize the most efficient instructions for your application to minimize program size while achieving the desired functionality.
3. Programming Language:
PLCs support multiple programming languages, such as ladder logic, structured text, function block diagrams, and sequential function charts. Each language has its advantages and disadvantages concerning program size and complexity. Choose the programming language that best suits your application requirements and programming expertise.
4. Hardware Limitations:
The hardware architecture of the PLC, including its processor speed and execution capabilities, influences the maximum program size. Higherend PLCs with faster processors generally support larger and more complex programs compared to lowerend models.
5. Modular Programming:
Divide your PLC program into modular sections or subroutines to manage complexity and optimize memory usage. Modular programming allows for easier troubleshooting, maintenance, and scalability of the PLC system.
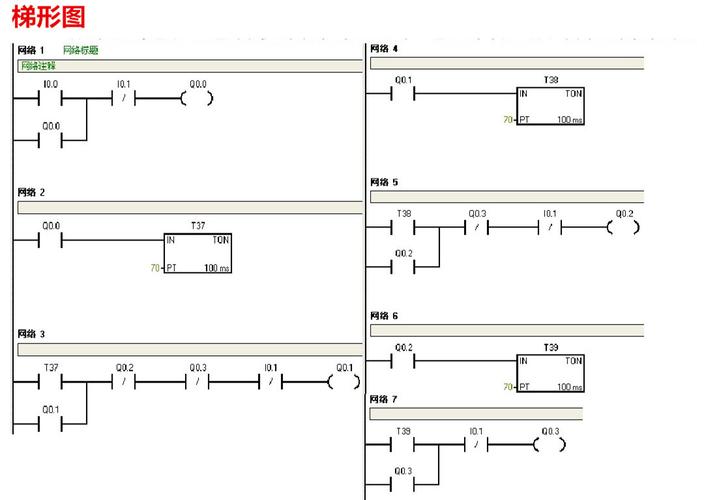
6. Optimization Techniques:
Implement optimization techniques to reduce the size of your PLC program:
Remove Unused Code:
Regularly review your program and remove any unused or redundant code segments.
Use Efficient Algorithms:
Choose efficient algorithms and data structures to minimize program size and execution time.
Optimize Communication Protocols:
Use efficient communication protocols and data formats to reduce data transmission overhead.
Simplify Logic:
Simplify complex logic by breaking it down into smaller, more manageable segments.7. Testing and Validation:
Thoroughly test and validate your PLC program to ensure it meets functional requirements while staying within the maximum programming capacity. Use simulation tools and test environments to verify program behavior and performance before deployment.
In conclusion, the maximum capacity of PLC programming depends on various factors, including memory capacity, instruction set, programming language, hardware limitations, modular programming, and optimization techniques. By understanding these factors and employing best practices, you can effectively maximize PLC programming to meet the demands of your industrial automation applications.